Having this kind of machine in your factory would solve numerous operational challenges to which manufacturing companies are exposed every day, such as lack of workforce, the need for increased production flexibility, continuous improvement of product quality, and reducing manufacturing costs.
A highly intelligent automated workforce was one of the key “smart” solutions that Kolektor sought to offer in the global market to transform their customer’s efficiency, flexibility, and manufacturing quality.
Our collaboration with Kolektor happened amid a global pandemic and a precarious business climate. That is why it was more important than ever to be flexible and demonstrate adept responsiveness to emerging challenges.
Inclusive approach from the start
We initiated our cooperation with a kick-off workshop, where contributors from both companies met for the first time. This was a crucial step for us since we could socialize as a product team, align on the challenges ahead, and exchange valuable insights on advancements in the industrial field.
Kolektor’s factory staff were willing to participate, joining us from their main manufacturing site in Slovenia. Direct input helped confirm or deny the team’s assumptions on the spot, leading to a super productive session.
The kick-off led to a field trip organized by our workshop guests. We familiarized ourselves with the production line in their facility, observed workers interacting with the R&D robot, and talked about their challenges and what could be done to prevent them. While designers detailed the use cases and visualized the user flows, the engineers clarified technical details about the robot, its cameras, connectivity, and security.
A rich conversation unfolded in situ about a sensible scope and first deployment of the minimal viable product, which was an essential step for us because it helped us understand what needed to be done to achieve maximum improvement.
Our key challenges identified
After gathering all the important information we began identifying primary circumstances that would indifenetly influence the development of our solution. Our conclusion brought several findings:
- Factory workers are skilled in their tasks but less so in robot handling. Helping them interact with robots in an accessible, friendly way is paramount to their productive relationship.
- Working on a global scale is a huge logistical and cultural challenge. The robot fleet would have to be mobile, remotely accessible for diagnostics, and speak multiple languages.
- Manufacturing facilities are, by design, very regulated environments. Implementing a cloud-based service and complete (remote) control over operations is impossible without an on-site presence.
- Kolektor Digital is a world-class R&D powerhouse. Putting the robots into actual use and scaling the fleet to production numbers required updating their practices and regulatory compliance.
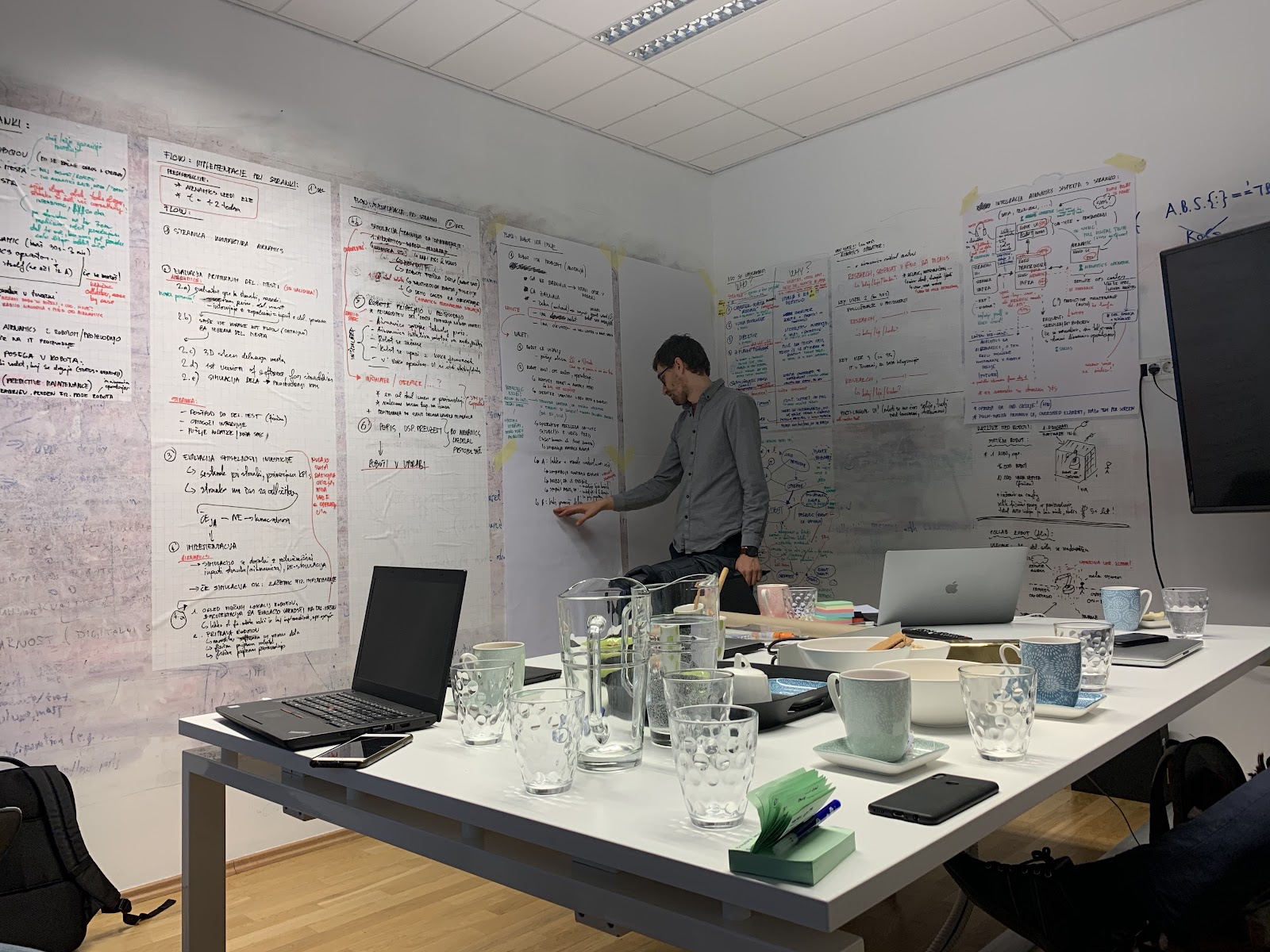
“It took everyone just over two weeks to clarify and align on what was actually needed. This would have been impossible without the early access to the actual users and their working environment.”
- Marko Jukić, Product & Team Lead, 3FS
Analyzing Kolektor Digital's R&D
Before transforming our ideas into reality, we first analyzed Kolektor Digital’s current R&D setup. We reviewed the existing source code and then suggested improvements to the software delivery pipeline, task management, and documentation. We tested the changes by developing an API for automated retrieval of images and videos from the robot’s onboard cameras.
As we delved deeper into the system architecture, several distinct parts of the system emerged.
First, we needed a system core running in the cloud, as the central relay for all robot connections, which would also save the robot telemetry and visual data. Exposing it through an API would allow us to build web applications for remote operation or preventive maintenance with relative ease.
Second, robots and their onboard operating system provided a software interface with the robot hardware but needed cloud connection capability and a custom onboard user interface to boot.
So we focused our efforts on critical points, utilizing a mock API interface and robot simulator so application development could proceed while the cloud infrastructure and the robot’s internal systems were catching up.
This decoupled approach kept various parts of the team moving at their own pace throughout our collaboration, even when the robots’ onboard application design slowed down due to the complexities of advanced features or when the robots’ operating system API had to be improved.
“One of the crucial aspects in developing our solution has been the handover to robot deployment teams. 3fs set a benchmark with their practices and swift response time.”
- Robert Bevec, Head Of Robotics, Kolektor Digital
Help Transforming Kolektor Digital's R&D
Kolektor Digital initially aimed for a cloud-connected, highly autonomous fleet overseen by remote operators through digital twins. However, due to security constraints in manufacturing, we refocused on human-robot interaction. Robots were set up as edge nodes, reducing cloud dependence for remote access. However distant access would still be possible, but limited to diagnostics and support, and only if requested and approved on-site.
Since human-robot interaction is complex, we thoughtfully designed and thoroughly tested it. The best time-saving approach was to do rapid prototyping methods: designers created highly realistic, interactive prototypes for each use-case, down to micro-interactions on the robot’s screen and the relevant state of auxiliary systems. Collaborative efforts with engineers and feedback from Kolektor Digital and factory staff helped us develop the best solution, avoiding costly changes in later production stages.
When we got to the most complex parts of the Robot UI – the robot programs and the operator dashboard with interactive widgets – it became clear that there wouldn’t be a one-size-fits-all solution. Numerous possible robot hardware configurations, an endless array of different production line workflows, and various customer preferences all need to be met. It was more sensible to redo our initial work in a modular fashion and continue building accordingly.
In the end, we delivered a bespoke design system, including tight integration with the robots’ onboard API. This required more planning and upfront effort but was ultimately justified with savings on configuration and support per each robot deployment, as Kolektor finally put the system they envisioned into actual use and is, at the moment, still operated independently.
After the project we have done some reflection on our work and recognized a few key points which were crucial for our success.
Key takeaways
- Having actual users participate as early as possible is invaluable! Had we not had access to factory staff from the kick-off onward, product development would take much longer, with more setbacks.
- Our solutions needed to focus on the UX (user experience) and the DX (developer experience): end-users in factories were not our only concern, but also the engineering staff at Kolektor Digital.
- Coronavirus pandemic, and the team’s geographical distribution, could have brought the initiative to a halt. Due to our remote-friendly Ways of Working and DevSecOps best practices, they haven’t.
- With transparency and adaptability comes excellent teamwork. We helped Kolektor Digital adopt new practices while accommodating existing tools and work in their robotics department.